Body Protected Electrical Area: Everything you Need to Know
- echo300
- 4 days ago
- 5 min read
The following content from TESTntel is provided as general information. TESTntel does not accept any liability for its accuracy or completeness. Visitors using this information do so at their own risk.
Patient safety is a top priority in any medical setting—especially where electrical equipment is involved. That’s why Body Protected Area (BPA) Testing is essential.
In this article, we’ll break down what BPA testing is, why it matters and how it’s done. We’ll also cover our medical equipment testing, which complements BPA testing for a complete healthcare safety solution.
What is a classified as a Body Protected Area?
Key Requirements in AS/NZS 3003
What Does the Testing Involve?
Who Needs BPA Testing?
TESTntel and Medical Equipment Testing
How Often Should BPA Testing Be Done?
Legislation & Standards
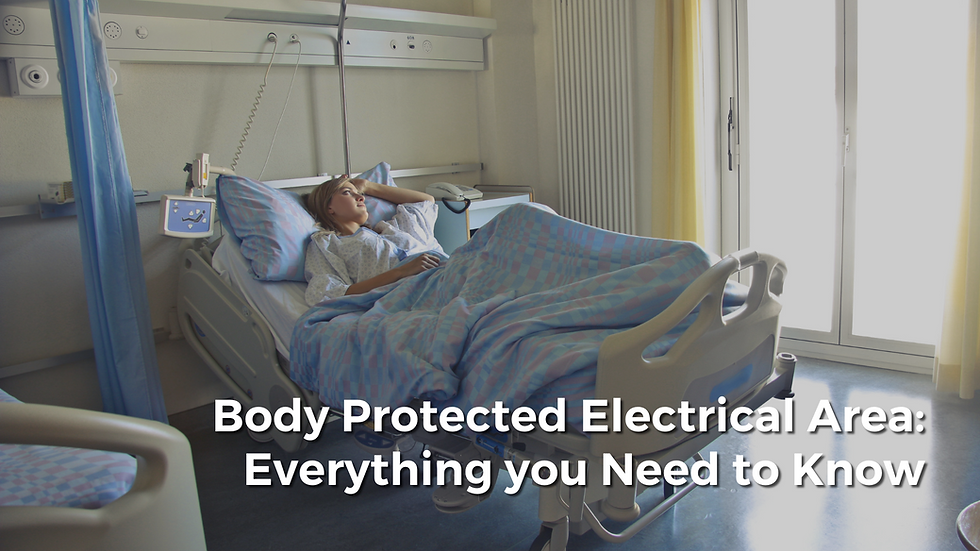
What is a classified as a Body Protected Electrical Area?
A Body Protected Electrical Area (often referred to simply as a Body Protected Area or BPA) is an area within a medical facility where patients are diagnosed, treated or monitored using medical electrical appliances.
According to AS/NZS 3003:2018 (the Australian/New Zealand standard for electrical installations in patient areas), the full list of Body Protected Areas may include:
(a) Accident and emergency wards.
(b) Allied health care providers, e.g. chiropractic, physiotherapy, optometry and naturopathic.
(c) Anaesthetic bays.
(d) Audiometry rooms.
(e) Blood collection areas.
(f) Day procedure theatres.
(g) Delivery suites.
(h) Dental surgeries.
(i) Dermatology rooms.
(j) Doctors consulting rooms.
(k) Endoscopy theatres and procedure rooms.
(l) General medical and surgical wards.
(m) High dependency wards.
(n) Imaging rooms.
(o) Nurseries.
(p) Operating theatres intended for non-cardiac surgery.
(q) Patient examination rooms for outpatients.
(r) Plasmapherisis areas.
(s) Plaster rooms.
(t) Recovery areas or wards associated with operating theatres and imaging rooms.
(u) Respiratory function laboratories.
(v) Resuscitation bays.
(w) Stress test rooms.
(x) Treatment rooms.
(y) Ultrasound rooms.

Key Requirements in AS/NZS 3003
While there are many requirements, the key ones include:
Medical-Grade RCD Protection: Every socket outlet within a Body Protected Area must be protected by a medical-grade Residual Current Device (RCD). These RCDs must be located within the area they serve, not in another room or just on the main switchboard. They must also be clearly visible, readily accessible and installed at a height of no more than 2 metres above floor level.
Related article: What is an RCD and how does it work?
Switched Socket Outlets: All socket outlets are located within the 2m of the entrance to the Body Protected Electrical Area and must be individually switched to allow for safe disconnection of equipment.
Clear Designation: The area must be clearly marked with a green Body Protected Area sign, indicating its classification and the need for enhanced electrical protection.

Appliance Testing:All electrical appliances used in the area—including both medical and general appliances—must be tested to meet AS/NZS 3551 standards.
Cleaner Circuit Requirements:There must be at least one separate socket outlet dedicated to cleaning equipment, which must be on a separate sub-circuit. This outlet must be clearly marked “Cleaning Purposes Only” and be located within 15 metres of the treatment area. In some cases, this outlet may be placed in another room or in a corridor.
Annual Certification:The entire Body Protected Area shall be tested and certified at intervals not exceeding 12 months, in accordance with AS/NZS 3003.
What Does the Testing Involve?
During the testing, our experienced technicians carry out the following checks using calibrated equipment to ensure accuracy and compliance:
Visual inspection of all outlets and controls, e.g. checks for damage, correct labelling, on/off indicators, illuminators and the number of outlets per RCD
Verifying and correcting circuit labelling
Checking outlet functionality
Ensuring correct installation of safety signage
Earth continuity testing on all sockets and fixed equipment
Measuring RCD trip times and testing audiovisual indicators
Checking prospective hazard current with Line Isolation Monitors
Record any faults or observations
Who Needs BPA Testing?
Hospitals (public and private)
Dental clinics
Radiology and diagnostic centres
Surgical or medical day clinics
Aged care facilities with medical equipment
Not sure if your site needs BPA testing? Our team is happy to provide a free consultation.
TESTntel and Medical Equipment Testing
We also offer Medical Equipment Testing to ensure your clinical devices are functioning. It includes:
Electrical safety testing and calibration of equipment like ECG machines, defibrillators, infusion pumps and other medical devices
Functional performance checks
Our technicians understand the sensitive nature of medical environments and always work with care and professionalism. Email us at medical@testntel.co.nz to learn more!
Why choose us?
Nationwide coverage with local-based technicians
Fast turnaround times to minimise disruption
Affordable, transparent pricing
Certified technicians experienced in AS/NZS 3003, AS/NZS 3551 and AS/NZS 3760
Detailed reports with images of tested item included
How Often Should BPA Testing Be Done?
Before Use – New patient treatment areas must be tested and certified before use
Routine testing – Every 6 to 12 months under AS/NZS 3003
After changes – Recertification are needed after any changes, renovations or installation of new equipment
The frequency may vary depending on your specific Health & Safety requirements. We can help you develop a tailored schedule to keep your facility compliant year-round.
Legislation & Standards
Below are the key standards that govern Body Protected Area Testing in New Zealand (links provided in the headings below):
This Act is New Zealand’s main workplace health and safety law. It requires all businesses (PCBUs) to do everything reasonably possible to keep workers and others safe. In medical settings, this includes making sure the environment is free from electrical hazards.
This regulation sets the rules for how electrical work must be done in New Zealand. This includes installing, testing and maintaining electrical equipment safely and to recognised standards. Testing Body Protected Areas and medical devices helps meet these legal requirements.
AS/NZS 3003 is the essential standard for electrical installations in patient areas of healthcare facilities. It defines what qualifies as a Body Protected Area and outlines which spaces are considered patient areas. The standard also explains the purpose of Body Protected Area Testing and includes a detailed testing checklist in its Appendix E to guide inspections and compliance.
AS/NZS 3551 outlines how medical devices should be maintained and tested to ensure they are safe and working correctly. Our Medical Equipment Testing service follows this standard to support clinical safety and reliability.
Although not specific to medical environments, this standard governs the general testing and tagging of electrical equipment in workplaces. It outlines procedures for inspecting and testing portable electrical appliances. It applies to non-medical items in healthcare facilities (e.g. computers, kettles and extension leads).
Related article: Understanding Electrical Testing and Tagging Compliance with Regulations in New Zealand
Body Protected Area Testing isn’t just about ticking boxes—it’s about creating a safe environment for vulnerable patients.
Partner with a provider you can trust. Our team is fully trained, equipped and ready to help you stay compliant with AS/NZS 3003. Call 0800 837 8824 for more information or to schedule a service.
Managing multiple sites? Our customer portal makes it easy to:
Track testing history
Full access to compliance report
Easy management across all your facilities
Comentarios